Alpitronic’s approach to charger reliability minimises downtime by doing as much as possible off-site. By Stewart Burnett
For electric vehicles (EVs) to gain mainstream acceptance, they must be as convenient to use as their internal combustion engine (ICE) counterparts. For years, the primary concern prospective owners have raised about EVs—beyond their cost—is the charging experience. Public charge point reliability is a particular concern among prospective and existing EV drivers alike.
A 2022 study by the University of California found that only 72.5% of the 657 public charge points in the Bay Area using the combined charging system (CCS) standard were functional. Additional studies have revealed similar numbers across the US. Despite the 84.6% average uptime self-reported by network providers themselves, a national study of 20,000 units by charger maintenance firm ChargerHelp calculated 73.7%.
Some countries have taken steps to improve charger reliability: the UK has implemented regulations mandating an average uptime of 99% across an operator’s entire network. The US has substantially less stringent standards. Instead of implementing a network-wide reliability target, the Biden Administration legislates that only one charger at a given location must be functional 97% of the time. Any effort to go above and beyond to meet US customers’ high expectations around reliability may need to come from the operators themselves.
Reliability on the backend
In September 2024, Italian charging firm Alpitronic officially opened its US headquarters in North Carolina. The 5,000-square-foot facility accommodates up to 300 employees, a customer demonstration site, a testing lab, and a repair centre. The company plans to use the new facility as a springboard to deliver what it describes as the “most reliable DC fast-charging stations” in the US market.
A variety of technological solutions converge on the company’s “robust” backend operation. The first and most fundamental aspect concerns live monitoring. “We have a proprietary system on our backend that allows us to remotely access every charger that’s currently live. This is very important from the perspective of reliability,” remarks Mike Doucleff, Chief Executive of Alpitronic Americas. This enables the company to immediately see and remotely diagnose the broad majority of issues with a given charger as soon as they appear. In practice, this means not having to wait until a consumer reports an issue to take action.
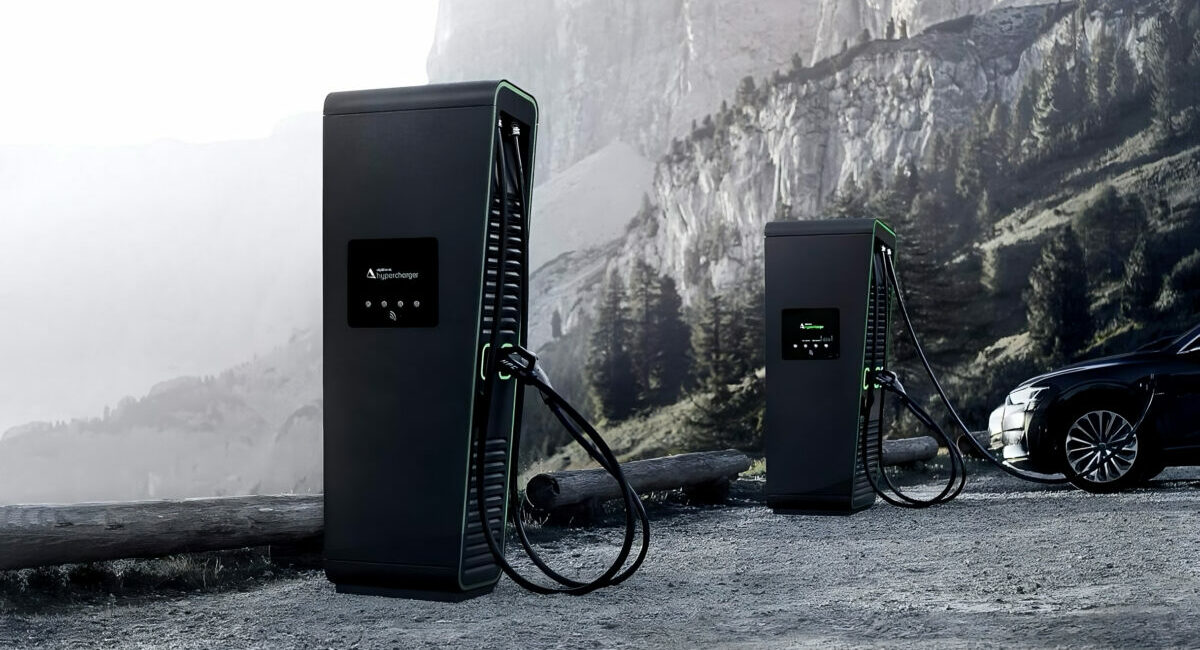
“Two-thirds of the time, we can identify and resolve issues straight from our 24/7 remote centre without needing to send a truck out,” Doucleff tells Automotive World. Generally, these repairs concern software errors that may require rebooting the OS or resolving connectivity issues with the payment system. The ability to “zoom out” and see the entire system operation in real-time also allows wider issues to become more obvious, allowing patches to be delivered as quickly as possible.
Doucleff notes that across its existing global network of 27,000 chargers, Alpitronic provides, on average, 160,000 charging sessions per day and more than one million per week. “We record every single one of them. Access to this kind of data is a key ingredient in reliability.” At the individual session level, the company can leverage this data to replicate the session in its grid simulator—effectively a digital twin of the real grid—and figure out what went wrong.
Alpitronic is considering further enhancing its backend operations by adding artificial intelligence (AI) to its data lake. With AI, the company believes it might be able to identify patterns in downtime, perform predictive maintenance, and even automate certain types of repair that might not require manual intervention. “Having the data is the starting point, and we are absolutely looking at how to leverage it better for future quality and reliability,” says Doucleff.
Onsite operations
While much can be accomplished through the backend to maximise charger uptime, roughly one-third of all repairs will still require a physical repair onsite. It is crucial to identify these cases as quickly as possible remotely in order to dispatch a team equipped with the correct tools and skills. However, it is also important to design the charging stations so that the onsite repair process is fast and easy.
“When we send a technician out to the field, they’re not bringing a soldering iron and changing individual components one by one,” explains Doucleff. “They’re swapping out the entire subassembly.” By using a modular approach, he believes a significant amount of time can be saved as, in addition to minimising the length of the actual repair, no onsite diagnosis is required. It can also reduce the potential for human error while conducting maintenance due to the simplicity of switching out an individual part.
There’s no kind of silver bullet for reliability
The subsystem that is switched out is then taken back to the repair centre for a thorough analysis of what went wrong. “We can learn a lot very quickly: is there a serial defect somewhere? Do we need to adjust our voltage range? It’s a far more efficient way to improve our quality and reliability processes than working it out onsite.” Tweaks can, in some cases, be made within the backend operation to prevent the incident from happening in future.
Doucleff is reticent to offer an opinion on government regulations around reliability but emphasises that the path towards such targets will require several approaches all at once. “There’s no silver bullet for reliability,” he emphasises. “It requires a combination of different technologies.” The common theme between these technologies, however, is a robust backend operation that maximises what can be accomplished remotely and streamlines onsite maintenance as fully as possible.