Krzysztof Wróblewski investigates molten salts, one of the most promising innovations for the tyre pyrolysis industry
The rubber and carbon black industries currently depend heavily on fossil fuel feedstocks. These industries urgently need alternative feedstocks that are low-carbon to meet investor and regulatory demands. Tyre pyrolysis remains a leading technology supporting these industries’ transformation to carbon neutrality. However, in recent years, tyre pyrolysis has been subjected to negative press regarding safety and environmental concerns. Is there a safer, more economical, and sustainable method for tyre pyrolysis? This question can only be answered through continuous innovation and investment in research and development (R&D).
Innovation and R&D are paramount to reaching the goals set out by the EU Climate Agenda and integrating these new solutions into the pyrolysis process.
The validity of molten salts
Through extensive investment into R&D, molten salts have recently been discovered as a medium to create conditions for a safer, more efficient, and economical production method during tyre pyrolysis, with repeatable product quality possible. Made from a commercially available salt mixture, they are a known technology with over seven decades of industrial application. They’re versatile and have several properties that make them suitable as a heat transfer medium in thermochemical processes such as end-of-life tyre (ELT) pyrolysis.
Generally speaking, molten salts are interesting and relevant because they’re chemically stable, have high heat transfer and storage efficiency, and have low vapour pressure. They use less energy than standard media to reach and maintain the high temperatures of 550 degrees Celsius needed for ELT pyrolysis. Since molten salts are solids at room temperature and melt to form liquids at high temperatures, they’re easily pumped through pipes to provide even and consistent heating to reactors containing rubber granules.
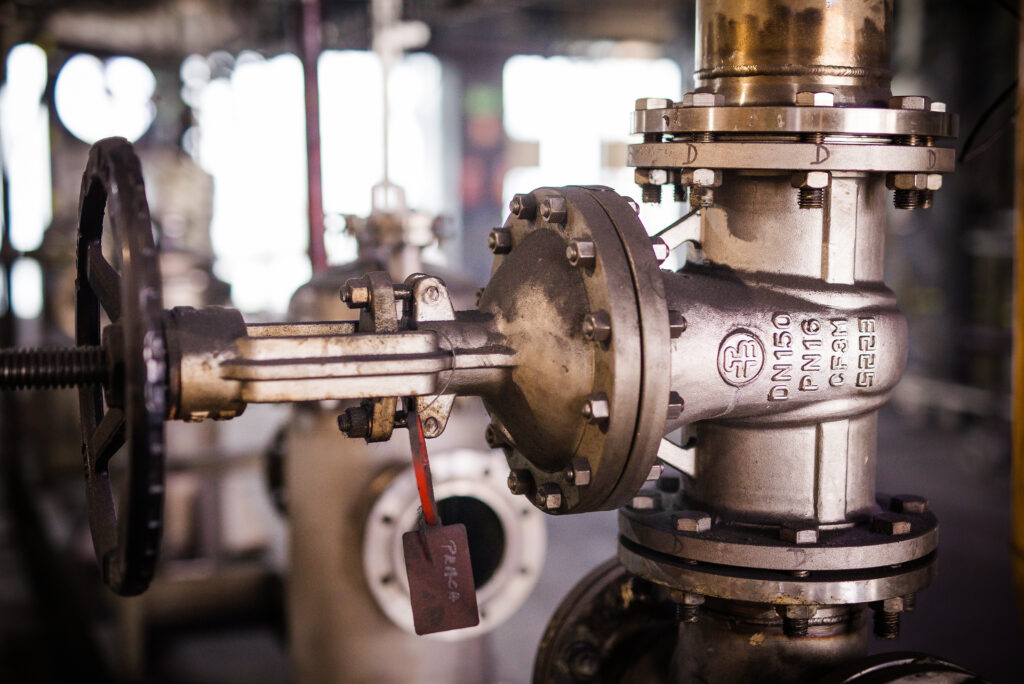
Heating the rubber in an oxygen-free atmosphere breaks down its complex plastic polymers to yield simpler chemical building blocks. This process treats all the ELTs uniformly, as no hotspots are formed, to produce high-quality circular and secondary products.
Molten salts’ low vapour pressure, even at high temperatures, eliminates the chance of gas pressure buildup in pipes, reducing explosion risk compared to other pyrolysis systems. Conventional pyrolysis plants have experienced explosions that are health- and life-threatening for workers and destroy plant facilities. Molten salts offer technical, economic, social, and environmental benefits that make them ideal for upscaling production and a good fit for the circular and sustainable economy.
In addition to integrating molten salts in pyrolysis, tire recyclers can also rely on multidisciplinary research and development, such as chemistry and engineering, to improve safety and product quality. Recent research, for example, led Contec to add an auger inside its reactor to rotate the ELT granules and ensure all materials were exposed to heat for the required time. Other novel pyrolysis techniques are also being tested to treat ELTs. Some focus on innovative heating methods like microwave-assisted pyrolysis (MAP) that uses molecular level non-contact heat transfer. Plasma pyrolysis introduces ELTs to a plasma or ionized gas, considered the fourth state of matter. Both techniques hasten the heating rate, improve energy efficiency, and ensure uniform heating. Reactor designs such as rotary kilns are other techniques that can guarantee uniform heating and heat transfer.
Continuous pyrolysis systems increase production efficiency compared to batch processes and are suitable for industrial upscaling. Fixed bed systems provide control over the process only at the laboratory scale and are unsuitable for upscaling. These innovative approaches to enhancing tyre pyrolysis were only possible through investment in R&D.
Tyre pyrolysis will only meet production safety, sustainability, and production demands through continuous innovation and R&D. Integrating molten salts is just one successful milestone in improving the pyrolysis process. Innovative leaders in the tyre industry cannot develop these innovations alone and must collaborate with other industry stakeholders, research institutes, policymakers, and funding agencies. Investment into R&D, innovation, and collaboration will pave the way to the successful decarbonisation of the tire and automotive industry.
The opinions expressed here are those of the author and do not necessarily reflect the positions of Automotive World Ltd.
Written by Krzysztof Wróblewski, CEO of Contec
The AutomotiveWorld.com Comment column is open to automotive industry decision makers and influencers. If you would like to contribute a Comment article, please contact [email protected]